In today’s embedded market, opportunities for emerging technologies have become a necessity. From more adept design-in solutions to entirely bleeding edge technologies, embedded systems thrive on “new.” One of the biggest vehicles driving these developments are Standard Development Organizations, or SDOs.
Many of these groups develop standards that are considered “open.” But, what does this mean?
An open standard is one that is readily available to the public and allows for adoption from any user for a variety of applications and end-uses. In brief, an open standard allows the technology to stay open and available for mass use.
This differs from a “corporate” or “de-facto” standard that may employ closed technologies only accessible to a select group.
Consider challenges upfront
While open standards offer many benefits, there are also several challenges in getting them off the ground and seeing them to completion. As would be expected, participation is crucial. Often, this involves much more than just attending and observing a meeting.
Active participation from various industry leaders is essential. The more people and perspectives that weigh in, the better the outcome. Without a diverse set of contributions from the working group, the benefits of being open are lost and progress can grind to a halt.
![]()
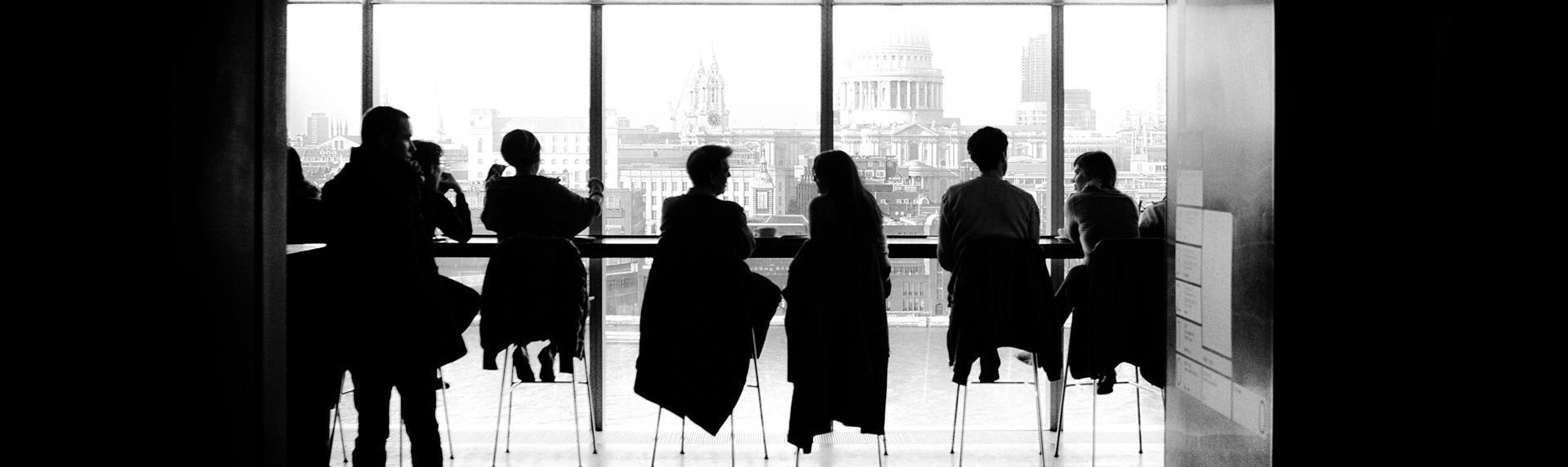
Many of the challenges facing SDOs today are easily overcome. And many are universal, not just contained to the embedded realm, but apply throughout technology initiatives. Here, we look at some of the most common ones that can obstruct open industry innovation.
Challenge 1: Not Being a Member of an SDO
While perhaps more obvious than some of the other challenges facing standard development, non-membership is one of the most common. Often, this can create insurmountable obstacles to participation, collaboration and ultimate completion of specifications.
Due to bylaws and potential NDAs, nonmembers often are denied access to documentation as well as voting rights. This can cause frustration, since an organization or individual may have valid points for consideration but are unable to voices their contributions. Beneficial concepts can be gone unheard.
The solution is simple; join the standard organization in question. Often, these consortiums offer a variety of membership tiers to fit a company budget and degree of participation. Even with associate-level memberships, companies are often able to gain access to important documentation, participate in group discussions as well as have voting rights. All of these are essential in standard development.
Challenge 2: Late Participation
Another challenge that often plagues organizations is late participation. At times, this is due to conflicting schedules and different interests during the time of development. Further complicating matters, late participation often arises from nonmembers having a limited ability to participate in an actively, timely manner.
Within certain organizations, many comments regarding finalization of a spec may arrive during the final stage of development. In the case of VITA, this would be during the ANSI vetting process.
While the concerns presented may be valid, the result may not prove ideal. Often, these late contributions set back the vetting process, causing significant turnaround. One standard we worked on was delayed over six months due to late participation, causing considerable frustration across the group.
Getting involved early proves to be the best remedy. Being an active member of the organization and participating in the initial work group efforts, you ensure your position in the group. This supports not only the best interests of the community early on, but also the interests of your company or industry.
Challenge 3: Building a Solid Team
Let’s say challenges 1 and 2 have been bypassed and efforts to write a specification are underway. It’s no secret that teamwork is essential to keep the process moving forward. However, building a dedicated team may present a challenge.
To help ensure success, look to groups with existing solid teams. Standards such as IEEE, PCI-SIG, Gen-Z, and SOSA all have dedicated teams, with driven and dedicated members that have been present since the group’s beginning. It is also helpful to have a group with a varied background for a more well-rounded approach to new standards and technologies.
For example, in the embedded market, a standard development group could benefit from the experience of system designers, electrical and mechanical engineers as well as connector manufacturers. It’s also helpful to involve marketing and sales expertise as needed to rate a specification’s marketability.
Challenge 4: Lack of Interest
Try as we may, some communities may not be interested in the proposed specification. Others may want to see changes, but don’t have the bandwidth to support the effort. Both can lead to a lack of balance or eventual shutdown.
In these types of situations, community chairmen or officers may need to step in and draw a line, another reason a strong team is critical.
Often, these pitfalls can be avoided utilizing tools such as ballots to gauge the interest of the community, not only during, but even before a standards effort is undertaken. This approach determines interest and proper allocation of resources as well as avoids delegating all the development to one company or individual. It also helps identify what aspects the standard needs to address and potential road bumps in the standard’s development.
Challenge 5: Internal Conflict
A final challenge, internal conflict, could be potentially positive or negative, depending on the outcome, as it’s a natural part of any collaborative effort.
In the case of standards development, competitors may be working on the specification together, while trying to represent the interest of their companies. On other occasions, active members may not be able to “standardize.” This could mean not coming to a collective consensus or limiting the scope of the specification in question.
Without a quorum, progressive standards can often become derailed or stuck in an endless cycle. To resolve issues, difficult decisions may need to be made by those leading the group efforts. Different manners of conflict resolution can be employed such as comment resolutions, necessary meetings and leverage of the community-at-large.
Although some decisions may not satisfy the entire group, these may need to be made for the good of progress and the community. Often, these changes can be ratified at a later time.
Progress despite some challenges
It’s true, no standard development will be flawless. Most of the time, members may run into all five of these issues—maybe even more, depending on the circumstances. However, it’s important to realize the benefit of Open Standards in today’s embedded market.
The value of being open and fast-tracking developments can only work with active participation of all members.
More often than not, the benefits of driving these groups to completion far outweigh both the time and resources demanded. This results not only in new technologies for the industry, but in benefits that represent the interests of your company within a wide variety of specifications. The future of Open Standards is now, but only through active participation.